Your Dependable Membrane Switch Manufacturer for Factory Applications
Discovering the Production Refine of Membrane Switch for Various Industries
The manufacturing process of Membrane buttons is an intricate venture that demands precision and interest to detail. From selecting proper materials to implementing strenuous quality assurance measures, each step plays an essential function in making sure functionality. Numerous markets, including automobile and clinical, rely upon these elements for their distinct applications. Comprehending the details of this process discloses substantial insights into how these switches are produced and their impact across diverse fields.
Comprehending Membrane Switches Over: An Overview
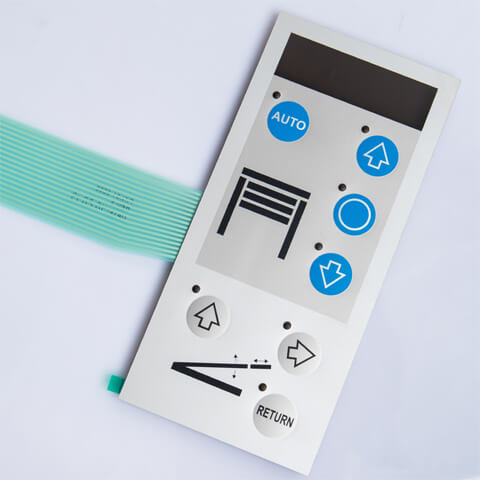
Secret Materials Made Use Of in Membrane Switch Manufacturing
In Membrane switch production, the choice of vital products considerably influences performance and resilience. Conductive materials, adhesives, and coverings play vital duties, while substrate option influences overall efficiency and reliability. Understanding these components is vital for maximizing the style and manufacturing of Membrane switches.
Conductive Materials Summary
Conductive materials play a crucial function in the performance of Membrane buttons, guaranteeing trustworthy electrical connections within the tool. Commonly used materials consist of silver, copper, and carbon-based inks, each offering unique advantages. Silver is preferred for its high conductivity and resilience, making it excellent for applications needing durable performance. Copper, while slightly much less conductive than silver, is an economical alternative commonly made use of in printed circuits. Carbon-based inks offer a versatile choice, appropriate for applications where versatility and lower costs are focused on, although they have actually lower conductivity compared to metal options. The selection of conductive materials directly impacts the total reliability, life-span, and performance of the Membrane button, making it an essential factor to consider in the manufacturing procedure.
Adhesives and Coatings
Coverings and adhesives are essential parts in the production of Membrane switches, giving essential bonding and protective residential or commercial properties. These products assure that numerous layers of the switch, including visuals overlays and wiring, adhere safely to each other, improving longevity and performance. Generally made use of adhesives consist of pressure-sensitive adhesives (PSAs) and epoxy-based formulations, which supply solid bond and resilience. Coatings, such as polyurethane or acrylic, serve to protect versus ecological variables, including moisture, abrasion, and chemicals. In addition, coverings can enhance responsive responses and aesthetic charm, contributing to the general user experience. The selection of suitable adhesives and coverings is important for optimizing performance and longevity in diverse applications across different sectors, guaranteeing that Membrane switches over fulfill certain operational needs.
Substratum Option Factors
Substratum selection plays an important function in the production of Membrane buttons, as it greatly influences their overall performance and sturdiness. Key materials such as polyester, polycarbonate, and flexible printed motherboard (FPCBs) are frequently made use of for their distinct buildings. Polyester is favored for its cost-effectiveness and resistance to abrasion, making it appropriate for applications with high wear. Polycarbonate offers premium clearness and influence resistance, perfect for environments requiring high presence. FPCBs supply boosted flexibility and are commonly utilized in complex designs. The selection of substrate additionally influences elements like thermal security, chemical resistance, and simplicity of printing. Inevitably, selecting the ideal substrate is vital for ensuring the performance and longevity of Membrane switches over across numerous sectors.
The Layout Process of Membrane Switches Over
The style process of Membrane switches is a crucial phase that considerably influences the functionality and visual appeals of the end product - membrane switch manufacturer. It starts with specifying the details demands of the application, including measurements, switch layout, and responsive responses preferences. Developers have to consider user communication, making certain that the switch is intuitive and accessible.Next, materials are chosen based upon longevity, versatility, and ecological resistance. The combination of graphics and branding components is also vital, as it enhances visual allure and communication. Prototyping allows for repetitive screening, allowing changes based upon user comments and performance evaluations.Additionally, the style needs to account for the electrical elements, such as circuits and adapters, making certain dependability and simplicity of use. Eventually, a successful design harmonizes functionality, visual appeals, and individual experience, leading the way for efficient manufacturing and durable efficiency in various markets
Printing Strategies for Membrane Changes
The printing strategies used in Membrane switch production play an essential function in figuring out the last item's top quality and capability. Screen printing uses benefits such as longevity and vibrant color application, while digital printing innovations supply flexibility and precision in design. Understanding these approaches can considerably influence the overall performance of Membrane buttons in different applications.
Screen Printing Advantages
Countless advantages make display publishing a favored technique for generating Membrane buttons. This approach enables premium, comprehensive layouts and vibrant shades, which are necessary for interface applications. Display printing is specifically effective for using thick ink layers, improving sturdiness and responsive comments. In addition, it provides superb attachment to different substratums, making sure longevity popular environments. The process is cost-effective for huge manufacturing runs, as it lessens arrangement time and waste. Display printing supports a broad range of inks, including specialized and UV-curable alternatives, allowing adaptability in style. Its capacity to produce consistent outcomes throughout several systems makes it a reputable selection for producers going for quality and performance in Membrane switch production.
Digital Printing Innovations
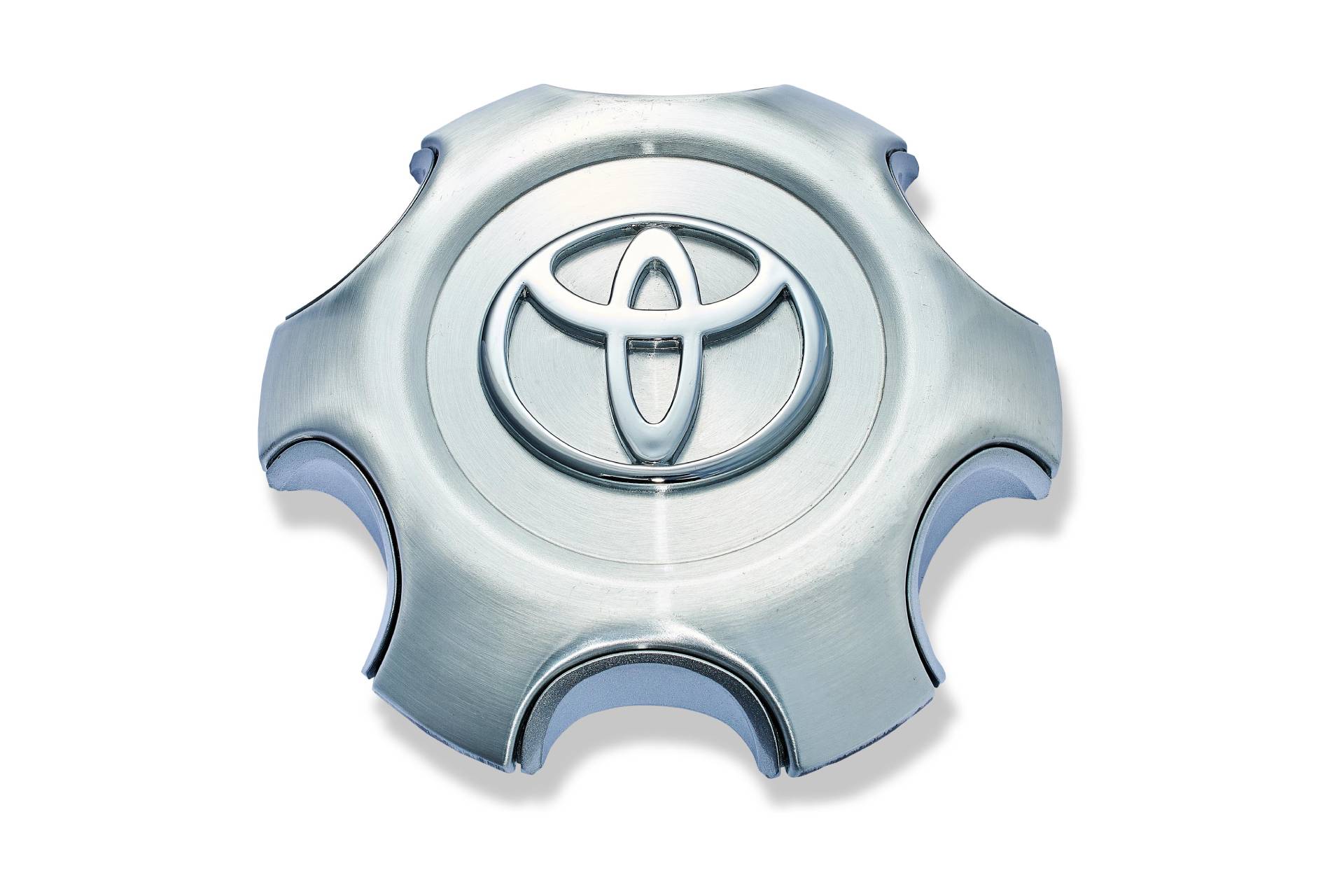
Developments in digital printing modern technology are transforming the production of Membrane buttons, using makers innovative services that improve layout versatility and effectiveness. Digital printing permits elaborate designs and high-resolution graphics, making it possible for custom-made branding and capability without the constraints of conventional approaches. This method decreases setup times and costs, promoting shorter manufacturing runs and minimal waste, making it perfect for businesses with differing demands. Additionally, advancements in ink solutions give far better resilience and bond, ensuring long life in different settings. As sectors significantly look for customized and complex styles, digital printing attracts attention as a crucial technique, establishing a brand-new requirement in Membrane switch production. The combination of these developments positions suppliers to satisfy developing market requires successfully.
Assembly and Layering of Membrane Switch Elements
Careful setting up and layering of Membrane button components are necessary to ensuring capability and toughness. This process starts with the precise alignment of various layers, consisting of the visuals overlay, sticky, circuit layer, and support material. Each element should be meticulously positioned to preserve electrical integrity and interface responsiveness.During setting up, conductive traces are used to the circuit layer, usually made from products like polyester or polycarbonate. This layer is crucial, as it transmits signals when pressure is used. The adhesive used for bonding these layers is additionally selected for its capability to endure ecological tensions while preserving a secure bond.Heat and pressure are typically applied during the setting up process to determine that the layers stick effectively without jeopardizing the performance of the switch. Attention is given to the side sealing to protect versus moisture and contaminants, protecting the longevity of the Membrane switch in different industrial applications.
High Quality Control Actions in Membrane Switch Manufacturing
Quality assurance actions play a vital role in making certain the reliability and efficiency of Membrane switches following the assembly and layering of their elements. In the manufacturing procedure, numerous vital assessments are carried out to promote quality standards. These include aesthetic evaluations for defects in printing and adhesive application, along with practical tests to verify the responsiveness of each switch.Additionally, environmental testing is performed to analyze the buttons' longevity against temperature level changes and moisture exposure. Producers commonly apply statistical procedure control (copyright) strategies to keep an eye on manufacturing uniformity, enabling very early discovery of anomalies.Furthermore, traceability systems are established to track components and products, making sure responsibility and helping with remembers if needed. Calibration of tools and adherence to market standards are additionally crucial to preserving item integrity. Jointly, these high quality control measures protect the basics efficiency of Membrane switches throughout various applications, eventually enhancing customer satisfaction.
Applications of Membrane Switches Throughout Different Industries
Membrane buttons are utilized throughout a diverse variety of sectors, showcasing their adaptability and flexibility. In the medical market, they supply reliable and waterproof interfaces for gadgets such as analysis devices and mixture pumps, ensuring health and simplicity of usage. The automotive market uses Membrane buttons for dashboard controls, look these up allowing smooth interaction in between the chauffeur and automobile systems.In consumer electronics, these buttons are located in appliances and portable devices, providing a sleek, modern-day aesthetic while enhancing capability. Industrial applications additionally utilize Membrane changes for machinery control panels, where resilience and resistance to harsh problems are essential.Furthermore, the aerospace and defense industries use Membrane switches for cabin instrumentation and interaction systems, focusing on reliability and performance under extreme problems. Overall, Membrane buttons play a crucial function in boosting the user experience and operational efficiency across numerous domains.
Regularly Asked Concerns
The length of time Does It Take to Produce a Membrane Layer Switch?
The production time for a membrane layer button generally varies from a couple of days to several weeks - membrane switch manufacturer. Variables affecting this period include design complexity, product schedule, and manufacturing volume, all impacting the overall timeline significantly
What Is the Regular Life Expectancy of a Membrane Switch?
The common life-span of a membrane layer button typically ranges from 1 to 5 million actuations, depending upon aspects such as worldly high quality, ecological problems, and usage regularity, significantly impacting toughness and overall performance.
Can Membrane Changes Be Customized for Particular Applications?
Membrane buttons can undoubtedly be tailored for details applications. Their layout adaptability enables changes in size, shape, shades, and graphics, making sure compatibility with one-of-a-kind needs throughout numerous industries and improving functionality and user experience.

Are Membrane Changes Environmentally Friendly?
The ecological effect of Membrane changes varies. Some materials utilized might not be environmentally friendly, while improvements in producing processes are progressively focusing on sustainability, intending to reduce waste and promote recyclable components in their manufacturing.
What Are the Common Failure Modes of Membrane Switches?
Usual failure settings of Membrane buttons consist of delamination, adhesive failing, wear and tear from usage, wetness ingress, and electrical failings. These issues can greatly impact capability, performance, and lifespan in numerous applications throughout various markets. Membrane buttons can be customized to fit details layout needs, such as shape, size, and capability, making them highly adaptable.The construction generally pop over here entails several layers, including a graphic overlay, sticky, and a circuit layer, which work with each other to produce a seamless customer experience. In Membrane switch production, the selection of essential materials significantly affects capability and sturdiness. The automobile market uses Membrane buttons for dashboard controls, allowing seamless interaction between the chauffeur and vehicle systems.In consumer electronics, these switches are discovered in home appliances and portable gadgets, offering a smooth, modern aesthetic while improving functionality. Industrial applications additionally leverage Membrane switches over for machinery control panels, where durability and resistance to severe conditions are essential.Furthermore, the aerospace and protection fields make use of Membrane buttons for cockpit instrumentation and communication systems, focusing on dependability and performance under severe problems. Membrane buttons can certainly be customized for details applications.